Profiling
Notching
Folding / Seaming
Bending
Slitting / Cutting
Special machines
Schlebach in perfection.
What makes our machines stand out
In the foreground of our company philosophy is the motto “Everything from a single source”. From the idea, the planning, the development and the production to the service: at Schlebach you will find everything under one roof. This guarantees you maximum performance with a high standard of quality.
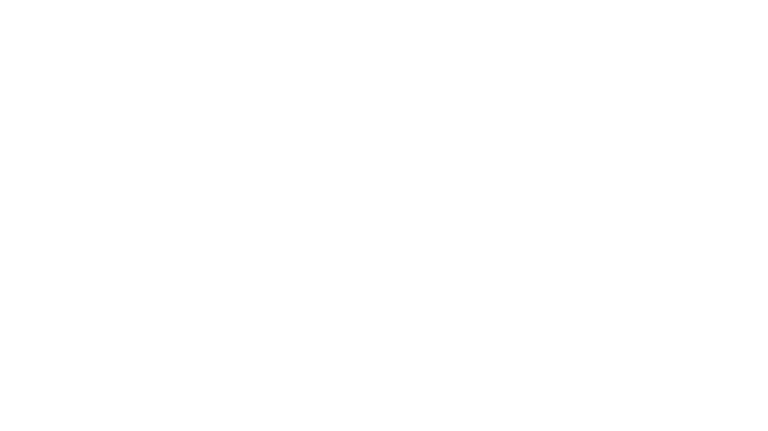
User-friendly
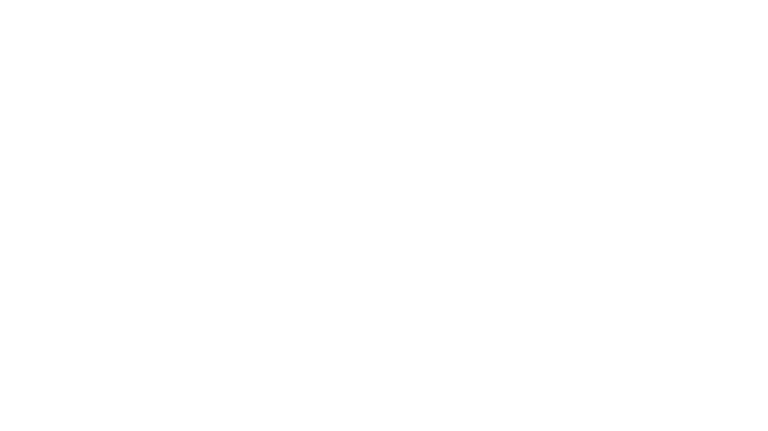
Powerful
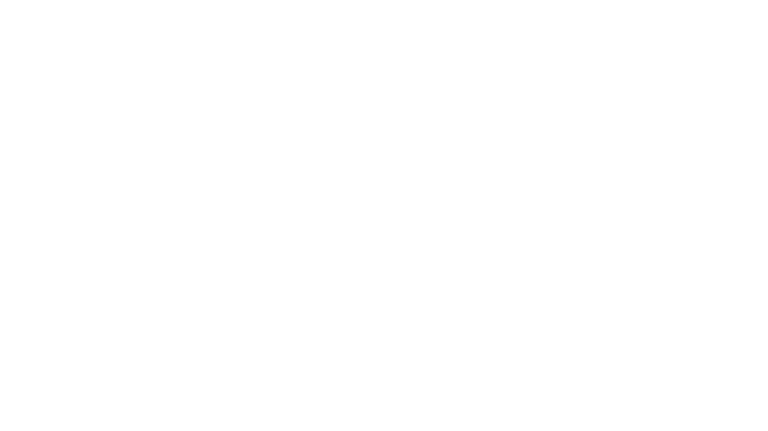
Maximum precision