The profiling machine QUADRO XXL is a versatile and multifunctional profiling machine with a max. infeed width of 1,250 mm. Similar to the proven system of the profiling machine QUADRO XL, it is also possible with the wider version QUADRO XXL to produce sheet metal profiles of the highest quality from a wide range of applications with only one basic machine in a user-friendly manner and with the shortest changeover time.
Thanks to the clever interchangeable cassette system, a wide range of different profiles can be produced economically on machines of the Quadro series. Very short changeover times by swiveling or exchanging cassettes.
Features
Quadro Serie
- Robust, versatile and multifunctional
- User-friendly PLC control with touch panel
- Stepless width adjustment 300 – 800 (1250/XXL)
- Low length tolerance of approx. 1-2 mm
- Feed rate 14, alternative 20 m/min
- Selection of a variety of roof and façade profiles / special profiles to meet customers’ wishes
- Exchangeable cassette system for short changeover times
- High profile quality thanks to the large number of forming stations
- Can also be used for single-sided passes for conical panels
- Electrically powered roller shears to perform cross cuts with automatic cutting
- Can be adapted to suit many applications thanks to extensive accessory range / additional modules
- Shortest panel length approx. 700 mm / depending on material and profile
- Optional cutters for panel lengths over approx. 100 mm
- Optional longitudinal cutter (LS) for producing fitting strips (see Quadro KS)
- Forklift pockets for safe transport
Quadro XL/XXL
- Extended base frame for holding pivotable cassettes with 12 forming stations
- Convenient pivoting of the cassettes using handwheel
- Reinforced roller shear for cross cuts
- Reinforced drive unit, optional feed rate 20m/min
- Run-in width of up to 1250 mm with XXL version
Video
Technical information
Supply voltage | 230 V / 50 Hz / 1 Ph. 230 V / 60 Hz / 1 Ph. 400 V / 50 Hz / 3 Ph. 400 V / 60 Hz / 3 Ph. |
Drive power | 2.2 kW |
Operating speed | Default: 14 m/min Optional: 20 m/min |
Infeed height | 900 mm |
Infeed width | 300 – 800 mm |
Shortest panel length | 700 mm (depending on material and profile) |
Length tolerance | approx. 1 – 2 mm |
Processable materials (profile dependent) |
Non-ferrous metals: Either 0.6 – 0.8 mm or 0.8 – 1.0 mm (has to be set before ordering) Non-ferrous metals: 1.0 – 1.2 mm (only with façade profiles) Steel (320 N/mm²): 0.55 – 0.70 mm Stainless steel: Max. 0.5 mm |
Dimensions (L x W x H) | 3,830 mm x 2,045 mm x 1,275 mm |
Weight | approx. 1,770 kg (with exchangeable cassettes) |
More information
In contrast to the QUADRO, the QUADRO XXL series can also be equipped with exchangeable cassettes with 12 stations on both sides with profile rollers. Thanks to this swiveling exchangeable cassette system with 12 forming stations, the changeover to a different profile takes place within the shortest possible setup times. This means that the Quadro XXL can be used effectively and economically for a wide range of even complex profile shapes with larger profile widths.
Thanks to the clever design, the customer is able to individually determine the equipment and thus the application range of the machine. Of course, the machine can also be retrofitted at any time with additional cassettes or extensive accessories.
The QUADRO XXL is built on a robust base frame and is designed to be mobile with 4 casters. Two casters can be fixed to prevent the machine from rolling away unintentionally. Furthermore, the crane lugs included in the scope of delivery and the forklift pockets attached to the frame enable safe transport of the machine on the construction site. This ensures flexible use of the machine both in operation and on the construction site. Hinged, gas-spring supported covers, which are secured by a safety device, protect the machine and the operator and facilitate adjustment work.
The infeed width can be infinitely adjusted between 300 mm and 1,250 mm using the proven manual spindle system via handwheel. In the infeed area, the QUADRO XXL is equipped with robust infeed guides with ball bearings on the right and left for stable guidance of the strip material. These are designed to be separately adjustable for adjusting the outer edges of the profile. This allows the strip to be fed smoothly and without play.
The additionally reinforced cross-cutting roller shear arranged in the infeed area consists of a cutting head with hardened roller blades which can be reground or even replaced with little effort if necessary. The cutting head is mounted on a maintenance-free linear roller guide and is driven by a toothed belt. This ensures a clean and burr-free cut. The shortest share length with this cutting process is approx. 700 mm within the shortest set-up times. This means that the Quadro XXL can be used effectively and economically for a wide range of even complex profile shapes with larger profile widths.
Due to the clever design, the customer is able to individually determine the equipment and thus the application range of the machine. Of course, the machine can also be retrofitted at any time with additional cassettes or extensive accessories.
The QUADRO XXL is built on a robust base frame and is designed to be mobile with 4 casters. Two casters can be fixed to prevent the machine from rolling away unintentionally. Furthermore, the crane lugs included in the scope of delivery and the forklift pockets attached to the frame enable safe transport of the machine on the construction site. This ensures flexible use of the machine both in operation and on the construction site. Hinged, gas-spring supported covers, which are secured by a safety device, protect the machine and the operator and facilitate adjustment work.
The infeed width can be infinitely adjusted between 300 mm and 1,250 mm using the proven manual spindle system via handwheel. In the infeed area, the QUADRO XXL is equipped with robust infeed guides with ball bearings on the right and left for stable guidance of the strip material. These are designed to be separately adjustable for adjusting the outer edges of the profile. This allows the strip to be fed smoothly and without play.
The additionally reinforced cross-cutting roller shear arranged in the infeed area consists of a cutting head with hardened roller blades which can be reground or even replaced with little effort if necessary. The cutting head is mounted on a maintenance-free linear roller guide and is driven by a toothed belt. This ensures a clean and burr-free cut. The shortest share length for this cutting process is approx. 700 mm.
The interchangeable cassette system is located in the profiling area arranged downstream. The swiveling cassettes with 12 profiling stations are accommodated there. The profile can be changed in a very short time by swiveling the cassettes or by changing the cassettes. Swiveling is performed with little effort by means of a handwheel via a transmission gear.
The changeover process takes only a few minutes and can be carried out quickly and easily without any additional aids. Auxiliary equipment such as a forklift truck, table crane or overhead crane is required to change the cassettes. But here, too, the maximum changeover time is less than 20 minutes. The hardened and surface-treated profile rollers of the exchangeable cassettes are preset at the factory for material thicknesses between 0.5 – 0.7 mm (exception: special or facade profiles optionally 0.6 – 0.8 mm or 0.8 – 1.0 mm). As with all Schlebach profiling machines, fitting shares, bevel shares and tapered shares can be produced easily and without auxiliary means in 2 working steps. The machine is equipped with a PLC for automatic processing of different lengths and quantities. The input is done via a menu-driven touch panel, which is located in the infeed area of the machine or optionally movable on a rail between infeed and outfeed area. The processing of the programmed profiling jobs can be fully automatic or in single cycle.
When profiling from coil, the desired length and number of pieces are first entered on the touch panel. The manually fed strip material is drawn into the machine by means of the driven transport rollers. Once the programmed length has been reached, the drive, which is controlled via a frequency converter, stops and the cut-off cut is performed automatically by means of driven roller shears. The overrun and thus the length tolerance is approx. 1 – 2 mm. In automatic mode, the restart of the next web is automatic. In single-cycle mode, the restart is triggered by the operator in each case. After the last profile web has been separated, further material feed can be stopped via a clutch lever and the belt can be retracted manually from the feed area.
Control variants
Hejm position controller (fixed programmed microprocessor control)
- Control panel with three-piece LED display
- 9 programs and each with 333 steps = 2.997 lengths and quantities can be free chosen
- Manual or automatic operation
- Single-step or continuous operation
- Zero cut manual with roller shear
- Program mode
- Working mode
Touch panel control (PLC)
- Control panel with 5,7 Zoll touch screen (STN / colored)
- 4096 displayable colors
- Resolution 320 x 240
- Multilingual menu language
- User-friendly operator interface
- 25 program memory locations with each 40 program steps
- Manual operation as jogging mode
- Automatic operation in single-step and continuous operation
- Setting-up mode
- Feeder speed continuously adjustable with the control panel
Touch panel control (PLC) with guide rail unit
- Control panel with 5,7 ” touch screen (STN / colored)
- 4096 displayable colors
- Resolution 320 x 240
- Multilingual menu language
- User-friendly operator interface
- 25 program memory locations with each 40 program steps
- Manual operation as jogging mode
- Automatic operation in single-step and continuous operation
- Setting-up mode
- Feeder speed continuously adjustable with the control panel
- Guide rail unit for comfortable operation of the control in the infeed or discharge area of the machine
Touch panel control (PLC) with guide rail unit
- Control panel with 10,4 ” touch screen (STN / colored)
- 4096 displayable colors
- Resolution 640 x 480
- Multilingual menu language
- User-friendly operator interface
- 25 program memory locations with each 40 program steps
- Manual operation as jogging mode
- Automatic operation in single-step and continuous operation
- Setting-up mode
- Feeder speed continuously adjustable with the control panel
- Guide rail unit for comfortable operation of the control in the infeed or discharge area of the machine
Accessories
Guideboy
Additional material guide for single-sided profile shaping of panels. The installation of the guideboy on any of the Schlebach profile shaping machine infeed guides requires little effort.
The Guideboy prevents the sheet material from shifting towards the centre of the machine during single-sided profile shaping operations. The required lateral force across the profiling direction may be adjusted by means of the directional angle, as well as an increase of the contact pressure on the sheet metal.
Damage to the material surface is ruled out by the use of high quality pressure rollers with a special rubber coating.
Slitting device LS
Slitting device for burr-free slitting of coil material before profile shaping. The LS can save time, especially when long standing seam sheets are being profiled from existing coil widths. This will also dramatically reduce the variety of coil widths that have to be carried in stock, which also results in a reduction in storage costs.
The cutting head is adjustable across the profiling direction to permit edge trimming of the infeed material to the required width. The blades of the cutting head are made of high quality tool steel to provide maximum service life. Because of the maintenance-friendly design, the cutting discs may be replaced or reground with very little effort when they have worn down.
Concave curving attachment
Concave curving attachment for the production of concave folded profile panels with a maximum height of 25 mm and a minimum bending radius of 3000 mm. The concave curving attachment is attached to the exit area of the profiling machine and is suitable for retrofitting. The folded profiles produced by means of the profiing machine is automatically fed to the concave curving attachment and bent to the desired radius by adjustable pressure rollers. The concave curving attachment consists of two bending assemblies, one for the side lacking overlap as well as one for the overlapping side of the profile.
Note: Concave curving is only possible at parallel profiled shapes.
Ribbing attachment 25 mm
Ribbing attachment to shape longitudinal ribs with a width of 25 mm and a depth of approx. 1.1 mm into the visible surface of profiled panels. The ribbing attachment consists of a guide unit, upper and lower ribbing rollers with brackets. The ribbing attachments are equipped with high-quality ribbing rollers on ball-bearings to ensure maximum protection of the surface of the panels being profiled. The ribbing attachments are continuously adjustable across the profile shaping direction. This ensures that the distance of the ribs that are pressed into the panels may be adjusted as required.
Note: The profiling of ribs is not possible on conical shapes.
Ribbing attachment 58 mm
Ribbing attachment to shape longitudinal ribs with a width of 58 mm and a depth of approx. 1.1 mm into the visible surface of profiled panels. The ribbing attachment consists of a guide unit, upper and lower ribbing rollers with brackets. The ribbing attachments are equipped with high-quality ribbing rollers on ball-bearings to ensure maximum protection of the surface of the panels being profiled. The ribbing attachments are continuously adjustable across the profile shaping direction.
Note: The profiling of ribs is not possible on conical shapes.
Pencil ribbing attachment
Ribbing attachment to shape round ribs with a width of 8 mm and a depth of approximately 2.2 mm into the visible surface of profiled panels. The ribbing attachment consists of a guide unit, upper and lower ribbing rollers with brackets. The ribbing attachments are equipped with high-quality ribbing rollers on ball-bearings to ensure maximum protection of the surface of the panels being profiled. The ribbing attachments are continuously adjustable across the profile shaping direction. This ensures that the distance of the ribs that are pressed into the panels may be adjusted as required.
Note: The profiling of ribs is not possible on conical shapes.
Striation unit
A striation unit to create small vertical striations with a width of 20 mm and an adjustable depth of 1 – 3 mm. The distance between the individual striation is at least 50 mm. The striation unit consists of a guiding unit as well as four upper and five lower striation rollers. Striation units are equipped with high-quality ball-bearing striation rollers that provide maximum protection to the surface of the profiled plates. The striation unit is continuously adjustable perpendicular to the profiling direction. This means that the distance between the striations that are impregnated into the plates is variable.
Note: The profiling of striations is not possible on conical shapes.
Punch for Soffit-panels
Punch for wall panels
Cross-cutting assembly QA60
Cross-cutting assembly for oblique cuts on profiled panels is made of non-ferrous metals. The assembly consists of a stable welded base frame, a swivelling table with carriage and a high-quality circular saw made by Bosch that is supplied with special blades for copper (type SBC with a hard chrome finish) or alternatively aluminium and titanium zinc (type SBS with steam-treated surface). The cutting angle across the profile shaping direction is continuously adjustable from 0° to ±60°. The connecting components required to flange the assembly to a profile shaping machine are delivered with the QA. The cross-cutting assembly can be installed after the profile shaping unit of different profile shaping machines. The existing length measuring device may be used.
Electrohydraulic notching unit AK-QUAD
Electrohydraulic notching unit AK-QUAD that is designed as an independent unit that is flanged on the QUADRO series of profile shaping machines or the special notching units to produce rhombic shapes, shingles or tiles. The notching unit is installed in front of the QUADRO profile shaping machine or it may be operated by means of an independent controller. The controller of the profiling system is programmed to support the notching sequence for the integration into the production process. The required tool holders along with the hydraulic equipment are installed on an additional unit that is connected to the QUADRO control unit.
The basic set includes a tool kit to notch Soffit panels (reveal panels). Tool kits are interchangeable and other types are available for specific shapes and profiles. We can produce tools to customer specifications. Available cut-out dimensions are 30 x 100 mm, 40 x 100 mm and 50 x 100 mm. The AK-QUAD can also be used as a standalone notching unit. With the appropriate tooling, the unit can cater for applications producing rhombic shapes, shingles or tiles.
Electrohydraulic notching unit AK-QUAD 4
Electrohydraulic notching unit AK-QUAD 4 that is designed as an independent unit that is flanged on the QUADRO series of profile shaping machines or special notching units to produce rhombic shapes, shingles or tiles. The notching unit is installed in front of the QUADRO profile shaping machine or it may be operated by means of an independent controller. The controller of the profiling system is programmed to support the notching sequence for the integration into the production process. The required 4 tool holders along with the hydraulic equipment are installed on an additional unit that is connected to the QUADRO control unit.
The 4 tool carriers can be utilised to produce notches on edge folds and 90° corner folds in a single pass.
The basic set includes a tool kit to notch Soffit panels (reveal panels). This consists of a set of tools to produce notches for edge folds, and a second set of tools to notch 90° corner folds. Tool kits are interchangeable and other types are available for specific shapes and profiles. We can produce tools to customer specifications. Available cut-out dimensions are 30 x 100 mm, 40 x 100 mm and 50 x 100 mm. The AK-QUAD can also be used as a standalone notching unit.
Bending station UKST
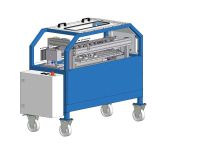
In addition, the bending station is equipped with its own control system and can therefore also be used independently for other bending processes such as rhombuses, façade clapboards/shingles, and coffers.
Foil laminating machine FBM
To bond acoustic barriers or insulating film as well as felt rolls to the plates during the profile shaping operation. The foil laminating system is compatible with the Schlebach profile shaping machines of the type SPM/PMC/SPA/PAC/QUADRO. The foil / felt material that must be bonded is clamped to a mandrel. With the help of a fork lift truck, the FBM may be loaded with the required rolls from the side. A built-in edge control system ensures smooth unwinding of the material with simultaneous precise bonding of the foil / felt to the bottom of the sheet metal. The pressure rollers mounted at the front apply the foil / felt material without bubbles. During bonding process, the protective foil on adhesive side of the foil / felt material is removed automatically and simultaneously wound on to a separate shaft.
Foil roller widths that may be processed: 150 mm – 730 mm
Max. Foil roller diameter: 280 mm
Inner / clamping diameter: 76 mm
Working height: 890 mm
Terminal voltage: 230 V / 50 Hz / 1 Ph.
Dimensions (L x W x H): 1750 mm / 1720 mm / 1150 mm
Weight: 700 kg
Suitable for the following materials:
Non-ferrous metals to 0.8 mm
Sheet steel up to 0.7 mm
Stainless steel up to 0.5 mm
Decoiler AH1250A1
A decoiler for metal coils with a max. weight of 1,000 kg and a max. coil width of 1,250 mm. The decoiler consists of a welded frame and a continuously adjustable mandrel on ball bearings with centre adjustment. The clamping range of the mandrel ranges from a min. of 280 mm to a max. of 530 mm inner coil diameter (optionally up to 650 mm). The manual braking assembly prevents metal coil overtravel. The decoiler is mobile because the decoiler is equipped with four swivelling castors. Extendable supports may be used to clamp the decoiler on site.
Decoiler AH1250K5
A decoiler for metal coils with a max. weight of 5,000 kg and a max. coil width of 1,250 mm. The decoiler consists of an exceptionally stable welded frame and a continuously adjustable mandrel on ball bearings with centre adjustment. The clamping range extends from a min. of 380 mm to a max. of 530 mm inner coil diameter. A standard braking assembly prevents metal coil overtravel.
Decoiler AH-PFL
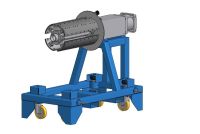
A decoiler with pneumatic clamping for metal coils with a max. weight of 2,000 kg and a max. coil width of 800 mm. The decoiler consists of a solid, welded base frame, and a pneumatically actuated floating mandrel (6 bar working pressure). Because of the one-sided, floating support, the decoiler may be loaded from the front by a forklift or crane. The clamping range extends from a min. of 380 mm to a max. of 420 mm inner coil diameter. The support plates that are supplied with the unit extend the clamping range of the mandrel from a min. of 480 mm to a max. of 520 mm. The max. permissible outer diameter of the coil is 1,100 mm. A pneumatic brake prevents any overrun of the metal coils. Four pneumatic cylinders can extend the castors when the decoiler must be moved manually. When the castors are retracted, the decoiler is placed on four stands, i.e. it is secured on site against it rolling away.
Decoiler TRANS-ASPO
The TRANS-ASPO uncoiler is for fast and simple holding of 1t coils. Due to the flying bearing and the manual height adjustment, the coil can be placed on the tensioning mandrel and tensioned manually without additional lifting equipment. The uncoiler is equipped with four travel rollers (two of which with fixing brake), and can therefore be placed easily in front of the working machine.
More products and solutions
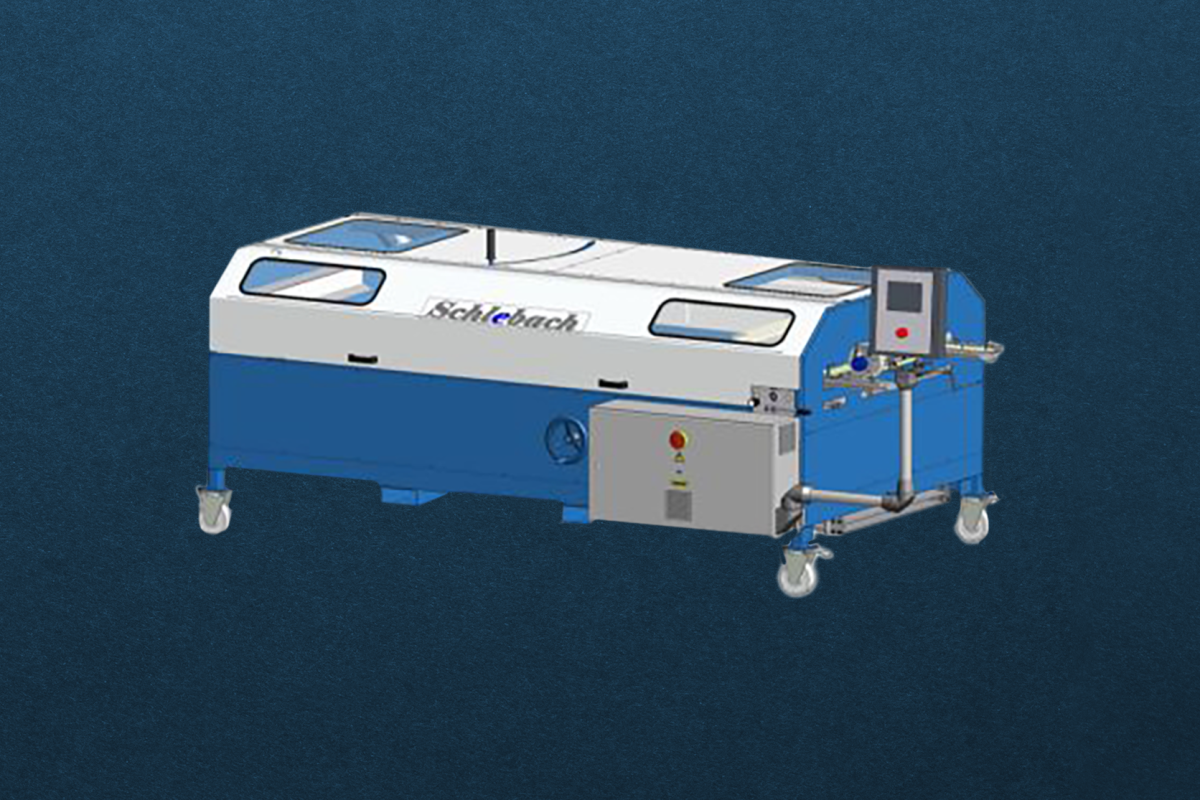
Profiling machine QUADRO-KS
Our profiling machine QUADRO-KS - For e.g. the economical production of long, conical profiled sheets for dome or tent roof shapes or also long conical fitting sheets
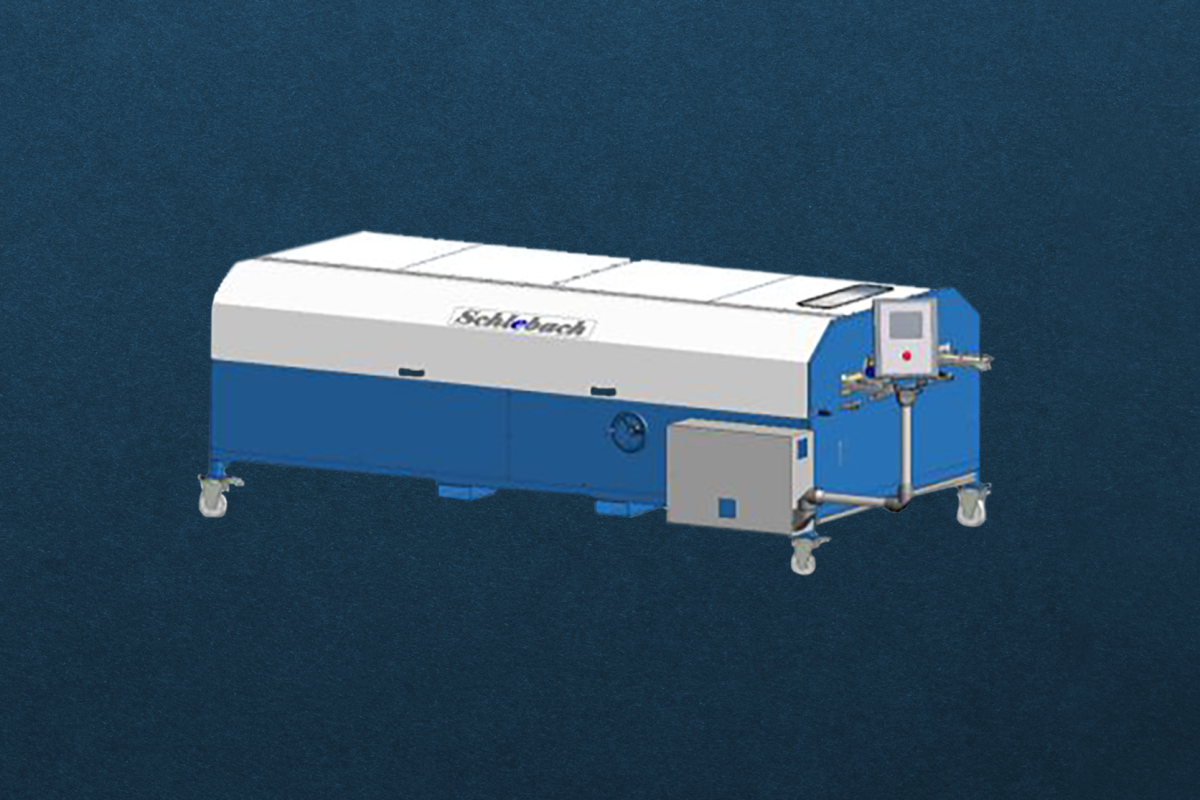
Profiling machine QUADRO-XL
Our profiling line QUADRO-XL - High-quality production of sheet metal profiles from the most different fields of application and with the shortest changeover time
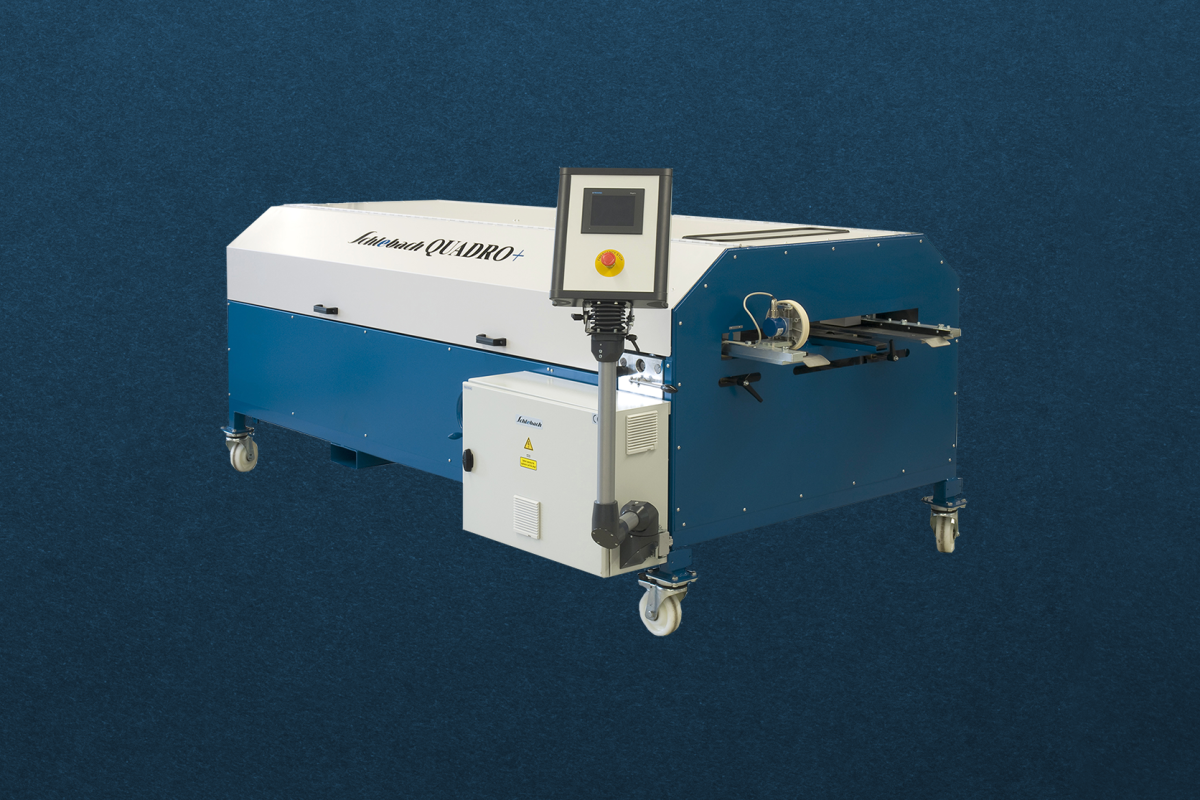
Profiling machine QUADRO
Our profiling machine QUADRO - For a wide range of profile variants, with exchangeable cassettes and 10 (swiveling) or 12 forming stations. Processing of sheet material or from coil up to 800 mm, with PLC and motorized roller shear.