The profiling machine MULTIPRO is a versatile and multi-functional profiling system for stationary operations. These basic machine can be utilised to produce complex high quality sheet metal profiles for many different applications in a user-friendly process and with a very short retooling times
The profiling machines exchangeable cassette system with 16 forming stations provide for very short retooling times for different profiles. This means that the MULTIPRO machine can be used effectively and economically for a variety of different profile shapes.
Due to the clever design, the customer is able to determine the equipment, i.e. the applications of machine on an individual basis. The machine may be extended with additional cassettes or with the vast range of available accessories at any time.
The MULTIPRO machine is supported by a robust base frame. Removable guards that are secured by a safety device protect the machine and the operator and simplify the adjustment procedures.
The infeed width is continuously adjustable from 300 to 800mm with the well proven system employing a spindle and a hand wheel. The right and left side of the MULTIPRO machines infeed area are equipped with robust infeed guides on ball-bearings that feed the strip material safely and securely. These are separately adjustable to adapt to the outer edges of each profile. As a result, the strip will run smoothly and without backlash.
The cross-cutting disc shear in the infeed area consists of a cutting head with hardened roller blades that may be sharpened or even replaced with little effort if necessary. The cutting head is mounted on a maintenance-free linear guide and it is driven by a toothed belt. This guarantees a clean, burr-free cut. The shortest panel that can be produces with this separation process is about approx. 1100mm.
As an option, the infeed area of the machine can be equipped with a revolving hole punch. This provides an economical way, for example, to punch a row of holes into the for attachment purposes.
The exchangeable cassette system is arranged in the profiling area. Depending on the type of profile it may accommodate the not rotatable cassettes with 16 profiling stations. Retooling for different profiles is accomplished in no time by replacing the cassette.
The replacement of the cassette requires tools such as a forklift or an overhead crane. Even in this case, the maximum time required is less than 30 minutes. The hardened and surface treated profile rollers of the cassettes are pre-set to material gauges of between 0.5-0.7mm in the factory (except for special or facade profiles they may be set to either 0.6-0.8 or 0.8-1.0mm). As with all Schlebach profile shaping machines, narrow panels, oblique panels and conical panels may easily be produced in just 2 operations and without additional tools.
The machine is equipped with a PLC to automatically process material in various lengths and quantities. Control inputs are entered via a menu-driven touch panel that is located in the infeed area of the machine. The program with the profile shaping runs may be executed automatically or in single cycle mode.
Profiling from a coil requires that the desired length and the item count are entered first via the touch panel. In the machine, manually fed strip material is transported by driven transport rollers. When the programmed length is reached, the frequency converter controlled drive is stopped and the crosscut shear executes an automatic cut. The overshoot, i.e. the tolerance in length is about 1-2mm. In automatic mode, the next strip is started automatically. In single cycle mode, the operator is responsible for the restart. When the last profile has been cut from the strip, the material feed may be stopped by means of the clutch lever before the strip is removed manually from the infeed area.
More products and solutions
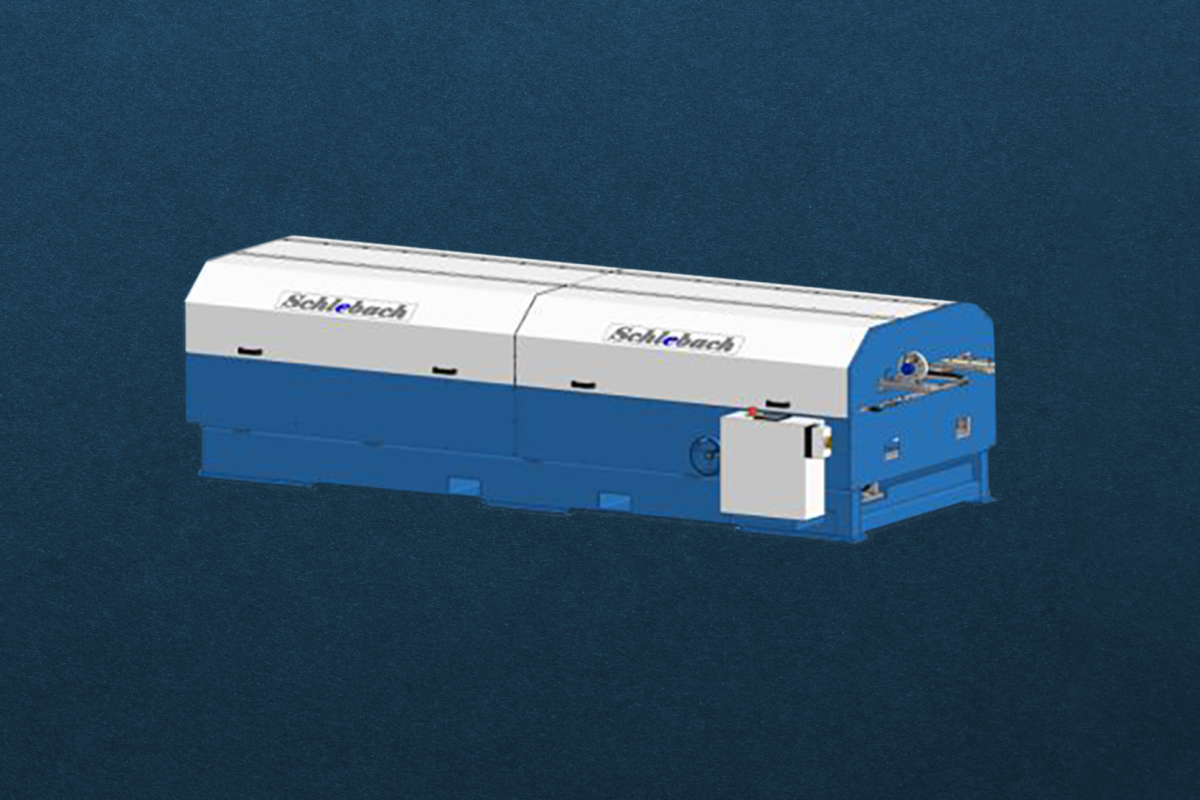
Profiling machine QUADFLEX
Our profiling machine QUADFLEX - A versatile and multifunctional profiling machine for stationary operation