facade panels
Laying
Planning
Unlike building facades that are based on double standing seam technology or other mechanical solutions, the panelling system technology requires detailed advanced planning because on-site corrections and changes can only be implemented with considerable effort. In addition to an appropriate sub-structure along with the selection of the associated fasteners, the facade must be divided into precise areas using accurate measuring techniques. In addition to the manufacturer’s instructions local standards and guidelines must be observed!
The classification in the light of overlap widths and shadow gaps should be entered into drawings and numbered, as they also serve as the basis for subsequent panel production in the workshop:
Planning also includes optimum positioning and anchoring of the scaffolding. Taking into account the local standards and guidelines in relation to occupational safety it must be ensured that panel installations require various scaffolding anchors to be released and moved, since these anchors cannot be enclosed until the final stages as, for instance, when installing panels.
Substructure
The requirements of the material manufacturer, system supplier and local standards and guidelines must be observed.
Manufacturing
In facade construction the production and assembly preparation is executed predominantly in the workshop and only infrequently on site.
Schlebach offers the machine program QUADRO as a flexible and affordable option for the economical production of the facade panels.
With replaceable cassette the QUADRO device produces the panels in a rollforming process.
For rectangular notching of bottom folds or corner notching for building corners where horizontal installations are being executed the notching station AK-QUAD is used, which is located in front of the QUADRO and linked to its control technology.
These operations can also be carried out in stand-alone mode when the notching station is disconnected. For short elements or for bevel cuts, for example, for the facade cladding a piloting cross-cut saw QA60 can be arranged in the outlet area of the QUADRO.
Connecting profiles and the finishing profiles are produced by means of folding presses or swivel bending machines.
During the production of facade elements it is necessary to consider that handling is limited to a minimum of manual interventions (e.g. through the use of pads and roller tables) to avoid unwanted distortion and damage.
In addition, the dimensional accuracy of the finished panels must be examined periodically to avoid dimensional and positioning deviations that occur during the linked assembly operations.
The protective film applied by the manufacturer should be removed immediately after installation.
Installation
The explanations presented below are examples only and may differ, depending on country-specific standards and guidelines. Schlebach does not accept any liability or give any guarantee for their validity, accuracy and completeness.
Mounting the connecting profiles
Before you can start the actual installation of panels you have to install the connecting profiles around window frames and other openings or corners.
If necessary, additional structural profiles may have to be affixed initially to the substructure for additional stability and to create additional mounting options.
Installation of the panels
Regardless of the installation type (horizontal or vertical) it is of particular importance to ensure that the orientation and position of the first panel is correct.
Panels that are installed horizontally must always be mounted from the top to the bottom to prevent water ingress at the joints.
The insertion side of any further panels is inserted into the pocket side of the installed panels and fastened to the side of the previously installed panel on the pocket side.
During the insertion you should work to the grid size and not to achieve even joints, as this may lead to creeping misalignments.
Generally, it is not necessary to insert additional sealing elements into the joints and connections.
To avoid creeping inaccuracies, the grid dimensions of the installed panels should be checked again after no more than three panels.
Use only screws and rivets that were tested and approved for construction as fasteners (see also par. substructure). Make sure you take the longitudinal expansion of the panels into consideration when you secure them in place (note material manufacturers details). For this purpose you can use the slots that were punched into the panels during manufacturing. You could also punch holes into the panels with a hand punch (e.g. sourced from M.A.S.C.).
To compensate for the longitudinal expansion on longer panels it may be necessary to insert a butt joint to limit the max. panel’s length (depending on the material, such as titanium-zinc having a max. length of 4 m). This serves as flexible intermediate element, which is usually prepared as a folded part and installed on the junction between the two faces of the panels.
At various connection points, on-going assembly can result in visible screw joints between the panels and the folded parts.
Installation of the finishing profiles
The same instructions apply to the finishing profiles as for the connecting profiles and other folded elements. Here additional structural profiles may be required to reinforce the substructure.
The final profiles may need to be combined with perforated plates to ensure adequate ventilation. Observe the manufacturers specifications for this purpose.
Repairs
Any damage to the facade may require a local exchange of elements. Here, each individual case must be examined whether disassembly from a connection point in close vicinity is worth the effort or if the damaged panels should be replaced with panels having custom-made folds. It may be necessary to use visible fasteners.
To prevent damage the use of edged corner profiles may be a better solution for building corners, especially at ground level. In some instances it may make sense to divide the facade further by means of intermediate elements.
Schlebach in perfection.
What makes our machines stand out
In the foreground of our company philosophy is the motto “Everything from a single source”. From the idea, the planning, the development and the production to the service: at Schlebach you will find everything under one roof. This guarantees you maximum performance with a high standard of quality.
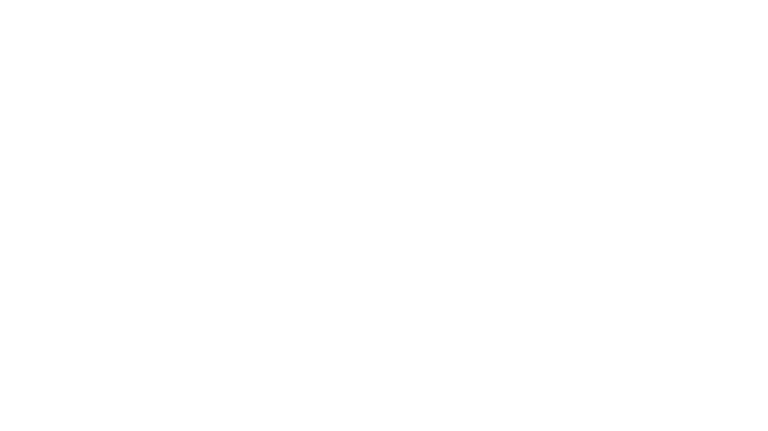
User-friendly
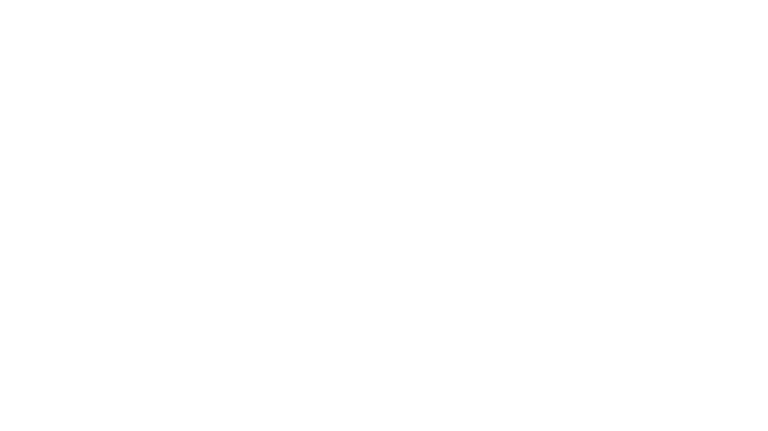
Powerful
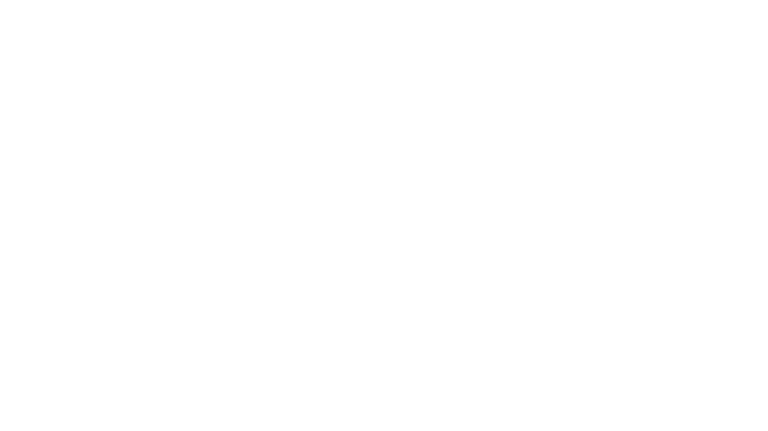
Maximum precision